En cualquier industria, la planificación es esencial para cumplir con los plazos de producción o entrega. En ese sentido, la Planificación de Requerimientos de Materiales (MRP) juega un papel clave al asegurar que los materiales estén disponibles en el momento adecuado.
Además, el MRP gestiona la demanda fluctuante. Al saber qué insumos se necesitan y cuándo, las empresas pueden organizar sus procesos de manera más eficiente, asegurando un flujo constante en la cadena de suministro en diversas industrias.
¿Qué es un MRP?
El MRP es un sistema clave para asegurar que los materiales estén disponibles en el momento justo. Su objetivo es evitar tanto el exceso como la escasez de inventarios, optimizando los costos y mejorando la eficiencia en las operaciones. Esto es fundamental en cualquier industria donde la producción o entrega depende de la disponibilidad de insumos.
Además, permite gestionar la demanda fluctuante, organizando los procesos de manera más precisa. Al saber qué insumos se necesitan y en qué cantidad, las empresas pueden ajustar sus planes y garantizar que los materiales lleguen en el momento adecuado.
Este enfoque no solo se aplica a la manufactura, sino también a otras industrias que dependen de una gestión eficiente de inventarios y recursos. Al mantener el flujo continuo de materiales, se mejora la capacidad de las empresas para cumplir con sus compromisos de producción y entrega.
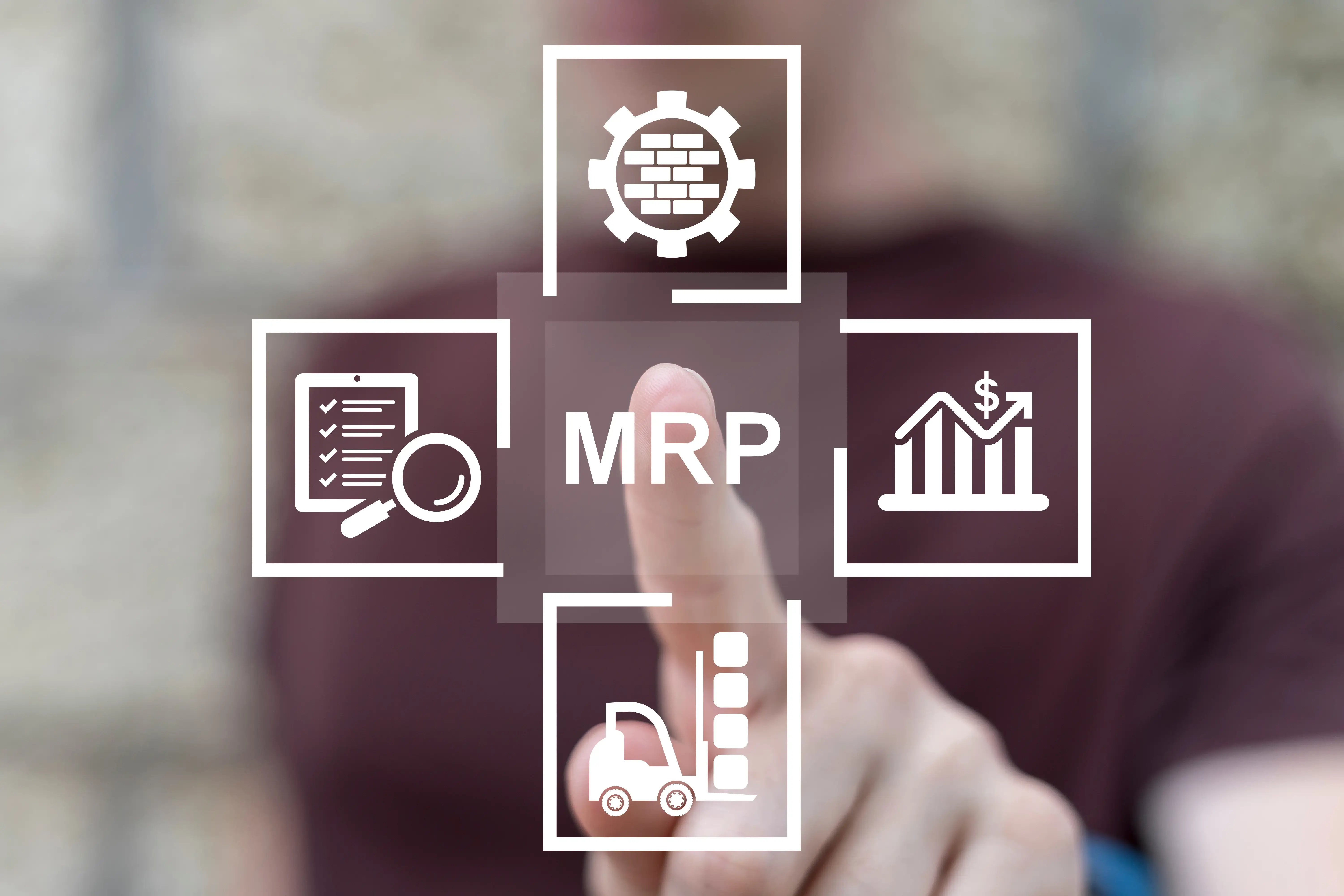
¿Cómo funciona el MRP?
El MRP se basa en tres elementos clave: la lista de materiales (BOM), el inventario disponible y el plan de producción. Estos componentes trabajan juntos para calcular los requerimientos de materiales.
El proceso empieza con la demanda del producto final y, a partir de ahí, se descompone en todos los componentes y materias primas necesarios para fabricarlo. A continuación desglosamos estas etapas:
Lista de materiales (BOM)
La lista de materiales (BOM) es un documento que detalla todos los componentes y materias primas necesarios para fabricar un producto final. Incluye desde las piezas pequeñas hasta los materiales principales, ofreciendo una visión clara del proceso de producción.
Además, especifica las cantidades exactas de cada componente, lo que ayuda a planificar compras y controlar el inventario. Esto asegura que no falten insumos y evita acumulaciones innecesarias.
Control de inventarios
El sistema MRP compara los materiales disponibles en inventario con los requeridos según la lista de materiales (BOM). Este proceso permite identificar qué insumos ya están disponibles y cuáles necesitan ser adquiridos, garantizando que solo se realicen pedidos para los materiales faltantes.
De esta forma, ayuda a evitar la acumulación innecesaria de inventario, lo que reduce los costos de almacenamiento y optimiza los recursos de la empresa.
Planificación de la producción
El plan de producción establece cuándo y cuánto se va a fabricar, sirviendo como base para que el MRP determine las necesidades de materiales. A partir de esta información, el sistema calcula las fechas exactas en las que cada componente debe estar disponible para cumplir con los plazos establecidos.
Gracias a estos cálculos, la empresa puede programar las compras y el aprovisionamiento de forma precisa, asegurando que los materiales lleguen a tiempo.
¡No te pierdas ninguna novedad en el mundo de la logística! Suscríbete a nuestro blog y recibe las últimas tendencias y consejos prácticos directamente en tu correo. ¡Súmate ahora y sé parte de nuestra comunidad!
Ventajas y desventajas de un sistema MRP
Ventajas de utilizar un MRP
Implementar un sistema MRP trae numerosos beneficios para las empresas. Entre las ventajas más destacadas se encuentran:
- Optimización del inventario: El sistema MRP reduce la cantidad de inventarios innecesarios al calcular exactamente lo que se necesita y cuándo se requiere. Esto no solo ahorra espacio y costos de almacenamiento, sino que también mejora el flujo de efectivo.
- Mejor control de la producción: El uso de MRP permite a las empresas planificar con antelación y asegurarse de que los materiales estén disponibles justo a tiempo para la producción, minimizando retrasos y garantizando que los plazos de entrega se cumplan.
- Reducción de costos: Al evitar la acumulación excesiva de inventarios y optimizar los procesos de compra, las empresas pueden reducir significativamente los costos de operación. Estos sistemas aseguran que los recursos se utilicen de manera eficiente, lo que impacta positivamente en los márgenes de beneficio.
.webp?width=1920&height=1080&name=MRP%20(1).webp)
Desventajas de utilizar un MRP
Aunque el sistema MRP ofrece importantes beneficios, también presenta algunas desventajas que las empresas deben considerar:
- Dependencia de datos precisos: El sistema MRP depende en gran medida de la exactitud de los datos ingresados. Si la información sobre inventarios o demanda es inexacta, puede generar errores en la planificación, afectando la producción o creando problemas de abastecimiento.
- Costos de implementación: La implementación requiere una inversión significativa en software, capacitación y posibles ajustes en los procesos. Para algunas empresas, especialmente las más pequeñas, estos costos pueden ser una barrera.
- Falta de flexibilidad: El sistema es menos efectivo en entornos de alta volatilidad o cambios rápidos. Las empresas con ciclos de producción muy cortos o demanda fluctuante pueden encontrar dificultades para adaptarse a los cambios con la rapidez que el mercado exige.
Cómo implementar un sistema MRP en tu empresa
Implementar un sistema MRP en cualquier tipo de organización requiere una planificación cuidadosa y ajustes. Sin embargo, una vez en funcionamiento, los beneficios son evidentes. Los pasos básicos para implementar un MRP incluyen:
-
Definición de objetivos: Antes de implementar el MRP, es esencial que la organización defina claramente qué objetivos busca alcanzar. Estos pueden incluir la reducción de costos de inventario, la mejora en tiempos de respuesta o la optimización en la gestión de recursos.
-
Recolección de datos: Para que el sistema funcione correctamente, es necesario disponer de información precisa sobre inventarios, recursos y necesidades futuras. Este paso asegura que las proyecciones de materiales y tiempos sean fiables, permitiendo una planificación más efectiva.
-
Capacitación del personal: La implementación de MRP supone cambios en la gestión de inventarios y recursos. Es fundamental capacitar al personal para que puedan utilizar el sistema de manera eficiente, asegurando que comprendan cómo integrarlo en los procesos diarios.
Desafíos del MRP
Aunque es una herramienta poderosa, su implementación no está exenta de desafíos. Algunos de los problemas más comunes que enfrentan las empresas al adoptar un MRP incluyen la precisión de los datos y la integración con otros sistemas empresariales.
Dependencia de datos precisos
El sistema MRP depende en gran medida de la precisión de los datos. Si la información sobre inventario o producción es incorrecta, el sistema puede generar errores, lo que podría provocar la falta de materiales o la sobreproducción.
Integración con otros sistemas
Las empresas que ya utilizan otros sistemas de gestión, como ERP (Enterprise Resource Planning), deben asegurarse de que el MRP se integre correctamente con ellos. La falta de integración puede generar duplicidad de tareas y errores en la planificación.
.webp?width=1920&height=1080&name=MRP%20(2).webp)
Para evitar conflictos es crucial alinear sus funciones y asegurar la coherencia de los datos en ambos sistemas mediante una integración adecuada.
Diferencia entre MRP y MRP II
El MRP original se enfoca únicamente en la planificación de materiales, garantizando que los insumos estén disponibles para la producción en el momento adecuado. Su principal función es gestionar los inventarios y evitar tanto el exceso como la falta de materiales en el proceso de fabricación.
En cambio, el MRP II amplía este enfoque, abarcando otros recursos esenciales para la producción, como la mano de obra, maquinaria y finanzas.
A grandes rasgos, el MRP se limita a los materiales, mientras que el MRP II integra todos los recursos necesarios para la fabricación, proporcionando una visión más completa de la operación, abarcando una planificación más global.
Diferencias entre MRP y ERP
Aunque MRP y ERP son sistemas que ayudan en la planificación y gestión de recursos, tienen diferencias clave. El MRP se enfoca principalmente en la planificación de materiales para la producción. Su objetivo es asegurar que los insumos estén disponibles en el momento adecuado, gestionando inventarios y tiempos de producción.
Por otro lado, el ERP (Enterprise Resource Planning) es un sistema más amplio. Además de gestionar los materiales, integra todas las áreas de la empresa, como finanzas, recursos humanos, ventas y distribución. Ofreciendo una visión completa de la operación empresarial.
En resumen, el MRP es específico para la producción y la gestión de materiales, mientras que el ERP abarca todos los procesos internos de una organización, proporcionando una mayor interconexión entre departamentos.
Conclusión
En resumen, el MRP es una herramienta esencial para las empresas que buscan optimizar su producción. Al proporcionar un control preciso sobre los materiales, permite reducir costos y mejorar la eficiencia en la gestión de inventarios, garantizando que los productos estén listos para satisfacer la demanda.
Si bien la implementación de un MRP requiere una planificación detallada e integración con otros sistemas, los beneficios a largo plazo, como una mejor gestión de recursos y una mayor capacidad de respuesta ante fluctuaciones de demanda, hacen que valga la pena el esfuerzo inicial.